Advanced techniques in carbon fiber insole production significantly enhance the durability and performance of insoles. By utilizing cutting-edge manufacturing processes, these techniques improve the structural integrity, comfort, and overall efficiency of carbon fiber insoles. Understanding these advancements helps consumers and manufacturers alike appreciate the benefits of modern insole technology.
Carbon fiber insoles are at the forefront of footwear technology, offering unmatched durability and performance due to their advanced production techniques. As the demand for high-performance and long-lasting insoles grows, manufacturers are adopting sophisticated methods to enhance the properties of carbon fiber materials. This article delves into how these advanced techniques in carbon fiber insole production contribute to superior durability and performance.
One of the primary advancements in carbon fiber insole production is the use of high-pressure molding techniques. This process involves applying high pressure and temperature to mold the carbon fiber material into the desired shape. The high-pressure molding enhances the density and strength of the carbon fiber, resulting in insoles that are highly resistant to deformation and wear. This technique also ensures that the insoles maintain their shape and structural integrity under various conditions, providing long-lasting support and comfort.
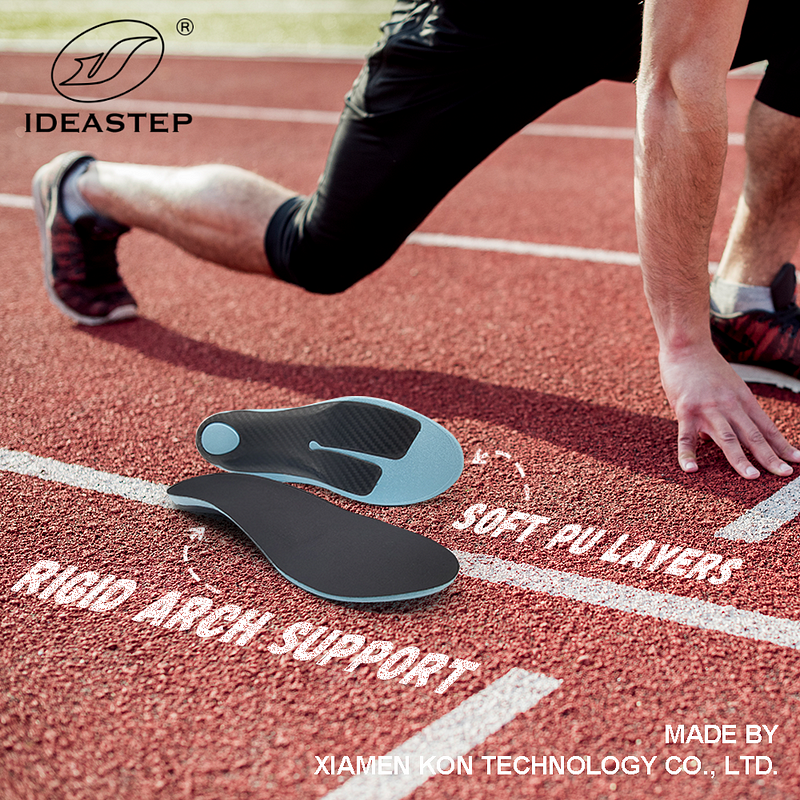
Another significant advancement is the incorporation of advanced resin systems. Modern carbon fiber insoles utilize epoxy or polyurethane resins that are specially formulated to bond with carbon fiber fibers. These resins enhance the overall mechanical properties of the insoles, including their flexibility, strength, and impact resistance. By improving the adhesion between the carbon fibers and the resin, manufacturers can produce insoles that offer superior performance and durability.
The integration of computer-aided design (CAD) and manufacturing (CAM) technologies has also revolutionized the production of carbon fiber insoles. CAD software allows designers to create precise 3D models of the insoles, optimizing the design for specific performance characteristics such as arch support and shock absorption. CAM technologies then use these models to guide automated production processes, ensuring high accuracy and consistency in the final product. This integration results in insoles that are not only durable but also tailored to meet the specific needs of users.
Advanced techniques in surface treatment further enhance the performance of carbon fiber insoles. Surface treatments such as laser etching and chemical coating can improve the insoles’ grip, reduce friction, and enhance their overall comfort. For example, laser etching can create textured patterns on the surface of the insoles to provide better traction, while chemical coatings can add moisture resistance and antimicrobial properties. These treatments ensure that the insoles perform optimally in various conditions and extend their lifespan.
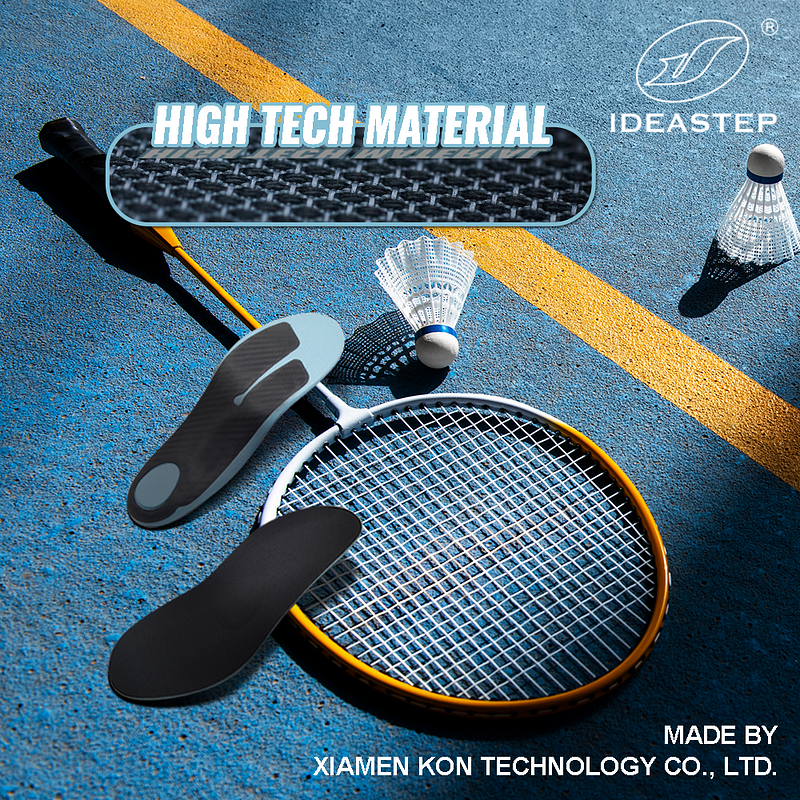
In addition to manufacturing advancements, the development of hybrid materials has also contributed to the improvement of carbon fiber insoles. Hybrid materials combine carbon fiber with other materials such as foam or gel to create insoles that offer a balance of rigidity and cushioning. This combination enhances the overall comfort and performance of the insoles, making them suitable for a wide range of activities and foot types.
Another noteworthy advancement is the use of automated quality control systems during production. These systems use sensors and imaging technology to inspect the insoles for defects and inconsistencies. By identifying and addressing issues early in the production process, manufacturers can ensure that only high-quality insoles reach the market. This automated approach helps maintain high standards of durability and performance in carbon fiber insoles.
In conclusion, advanced techniques in carbon fiber insole production, including high-pressure molding, advanced resin systems, CAD/CAM integration, surface treatments, hybrid materials, and automated quality control, significantly enhance the durability and performance of insoles. These innovations ensure that carbon fiber insoles provide superior support, comfort, and longevity, meeting the demands of modern consumers and athletes. As technology continues to evolve, further advancements in insole production are likely to offer even greater benefits.
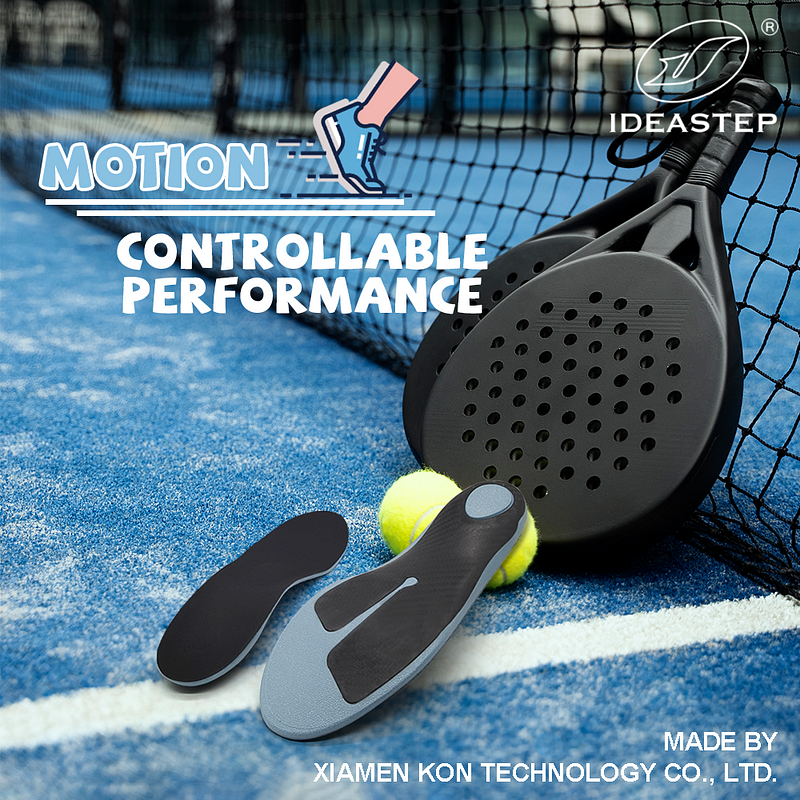
FAQ
1. How does high-pressure molding improve the durability of carbon fiber insoles?
High-pressure molding enhances the density and strength of carbon fiber insoles, making them highly resistant to deformation and wear. This technique ensures that the insoles maintain their shape and structural integrity over time.
2. What role do advanced resin systems play in carbon fiber insoles?
Advanced resin systems, such as epoxy or polyurethane resins, improve the mechanical properties of carbon fiber insoles. They enhance flexibility, strength, and impact resistance by improving the adhesion between the carbon fibers and the resin.
3. How do surface treatments enhance the performance of carbon fiber insoles?
Surface treatments like laser etching and chemical coatings improve grip, reduce friction, and enhance comfort. Laser etching provides better traction, while chemical coatings add moisture resistance and antimicrobial properties, ensuring optimal performance in various conditions.