How Carbon Fiber Insoles are Made: A Step-by-Step Guide
Carbon fiber insoles are known for very vast strength, light weightedness, and excellent durability. The insoles are predominantly used by athletes, those who have problems with their feet, and all those looking forward to attaining better performance and support from their shoes. But how do these insoles, which are state-of-the-art, make? This step-by-step guide will give a closer look at the process in making carbon fiber insoles.
Step 1: Designing the Insole
From design, the journey of a carbon fiber insole starts. Each foot is special, and so are the requirements of people needing these insoles. Often, the process is initiated after an in-depth analysis of the user’s foot shape, arch height, and gait. For custom insoles, this might involve 3D scanning or casting for an accurate model of the foot.
Designers work for a perfect blend of support, flexibility, and comfort in an insole. In the case of mass-produced insoles, even though the design is based on strict testing, it is based on average shapes and dimensions of the feet.
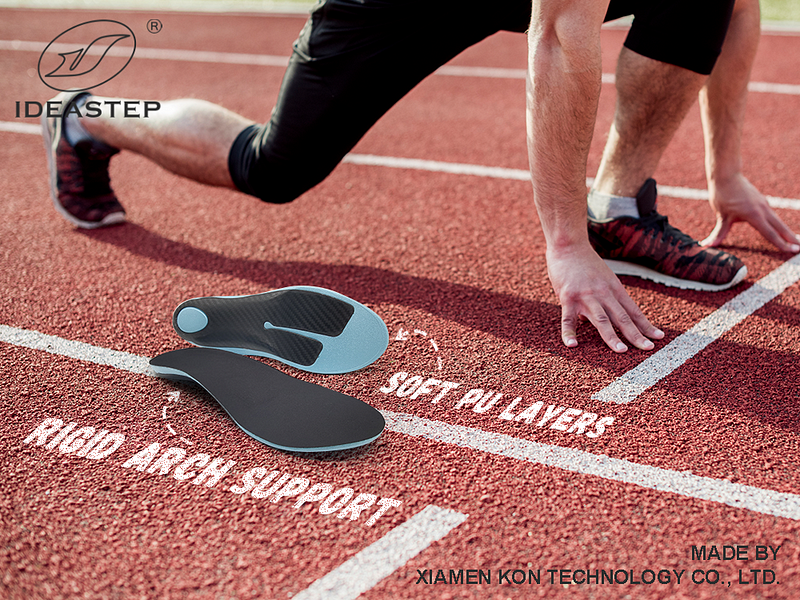
Step 2: Selecting the Materials
It’s carbon fiber all the way with these insoles. The material is selected for a phenomenal strength-to-weight ratio; it is, therefore, incredibly strong yet remarkably light. This consequently results in its effectiveness when fixed into insoles, providing the support needed with durability yet saving weight where it’s not needed.
Used with carbon fiber are many other materials, including resins, foams, and fabric. Resin is arguably the most important because it binds the carbon fibers together in order to provide some kind of form to the insole. In combination, these materials would resonate structure, and comfort while adding performance to the insole.
Step 3: Cutting of Carbon Fiber
Cutting of the carbon fiber sheets into shape follows once the design and materials are ready. This is a process that demands accuracy and carefulness. The carbon fiber sheets are usually laid in layers, and then each layer is cut accordingly to the design of the insole.
Accuracy is achieved with the use of advanced cutting machines, most of which are laser-guided. The number of layers may differ depending on the level of support and stiffness desired in the insole. Generally, more layers mean a stiffer insole, which can be useful for athletes or people who require additional support.
Step 4: Molding and Shaping
The carbon fiber sheets are cut and then molded into the insole shape. This is achieved through the application of both pressure and heat. The layers of the carbon fibers are placed into a mold lying in accordance with the design of the insole. After that has been done, high heat is applied to the mold, which then activates the resin to become pliable.
Pressure is applied until the carbon fiber conforms to the shape of the mold. As this step is carried out, the shape of the insole needs to be appropriate for the intricate contours of the foot and, at the same time, not compromise on rigidity. This leads to a solid form of carbon fiber insole that has been shaped to perfection and, therefore, will provide support in the critical areas.
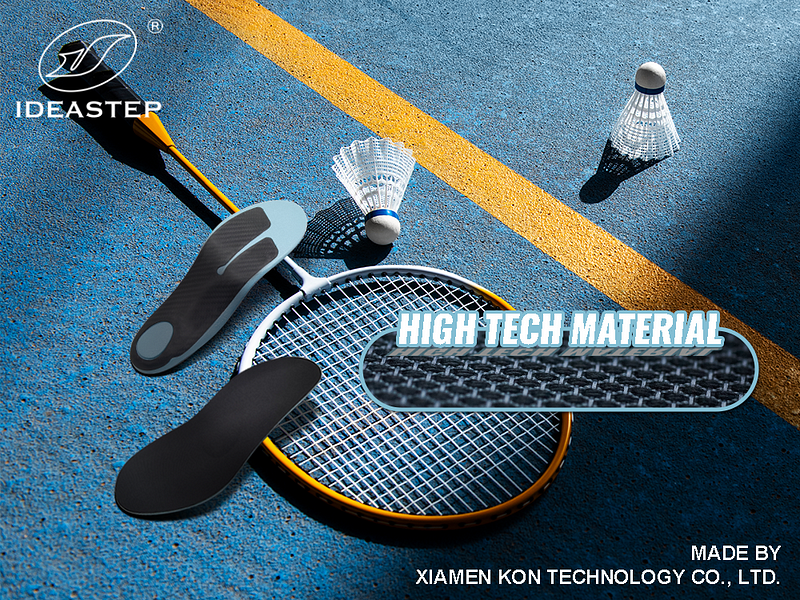
Step 5: Finishing and Curing
Immediately after shaping, a carbon fiber insole must be cured. More or less, curing can be considered the hardening phase of the insole while it cools and sets. This will ensure that the insole retains its shape and is durable. This step could last several hours according to the type of resin.
This is then extracted from the mold and completed. This includes finishing off with trimming of any excess material in the insole, after which the edges are sanded to ensure the finishing is smooth and that any additional layers or features added, such as paddings or top covers, are put. This is to make the insole functional and comfortable for use.
Step 6: Quality Control
The carbon fiber insoles undergo a rigorous filling quality control process before being packaged and consolidated for shipment. Every insole is examined for defects — got those that include cracks, uneven surfaces, and incorrect sizing. The insoles are also submitted to tests to ascertain performance characteristics in the major areas: flexibility, durability, and comfort.
Final adjustments can be made to custom insoles to ensure the insoles match the user’s needs. When the insoles have passed the various quality tests, they are said to be prepared fully.
Step 7: Packaging And Distribution
The packaging of carbon fiber insoles is the last stage of production. They are packed with ultimate care to make sure that they cannot be destroyed when in the process of shipment. The packaging sometimes can contain instructions for use and care in general, especially for tailor-made insoles that might require some kind of special care.
After they have been made, the insoles are then supplied to retail, medical professionals, or directly to the consumers. Companies like Ideastep, who manufacture custom orthotics and insoles, take many measures to protect them in the packing so that they can be in perfect shape when they reach the consumer and deliver the promised support and ease.
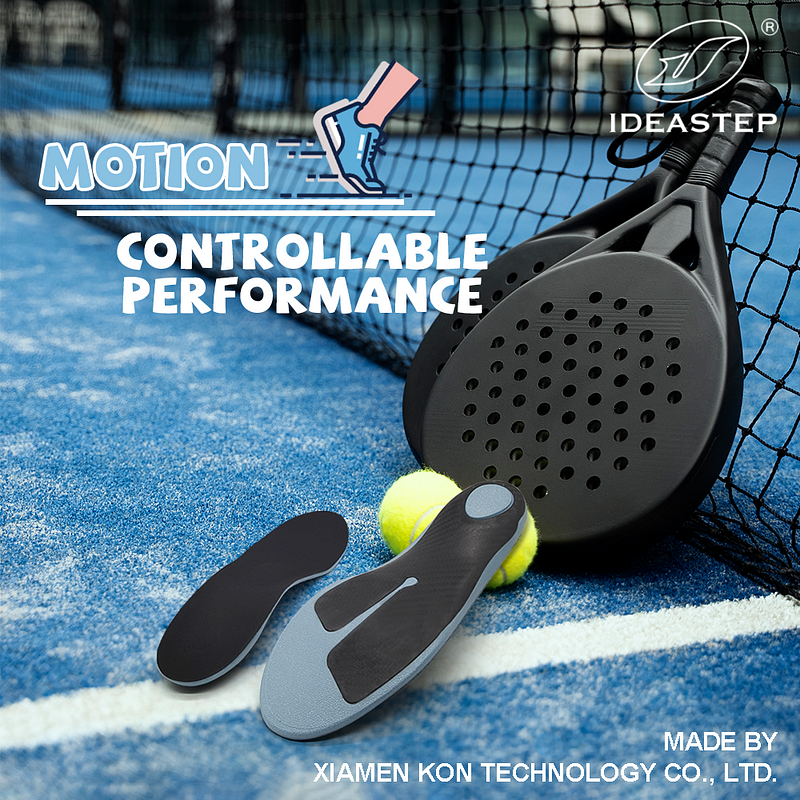
FAQ
Q: How long does carbon fiber insole last?
A: Under normal wear, carbon fiber insoles should last 1–2 years. Individual usage and circumstances obviously influence this greatly. Athletes or those who use them heavily on an everyday basis will need to replace them sooner.
Q: Can carbon fiber insoles be used in your everyday footwear?
A: Carbon fiber insoles can be used with most forms of footwear. However, they are most beneficial in cases where the footwear used involves more athleticism and extra support, such as athletic shoes and boots. Carbon fiber insoles can be custom-tailored to fit the specific shoe.
Q: Will carbon fiber insoles help foot pain?
A: Carbon fiber insoles provide the best arch support, hence helping with the aches from plantar fasciitis, flat feet, or high arches that result in pain in the feet. Not only will it provide supportive benefits, it’s also a highly recommended add-on by podiatrists for other support.